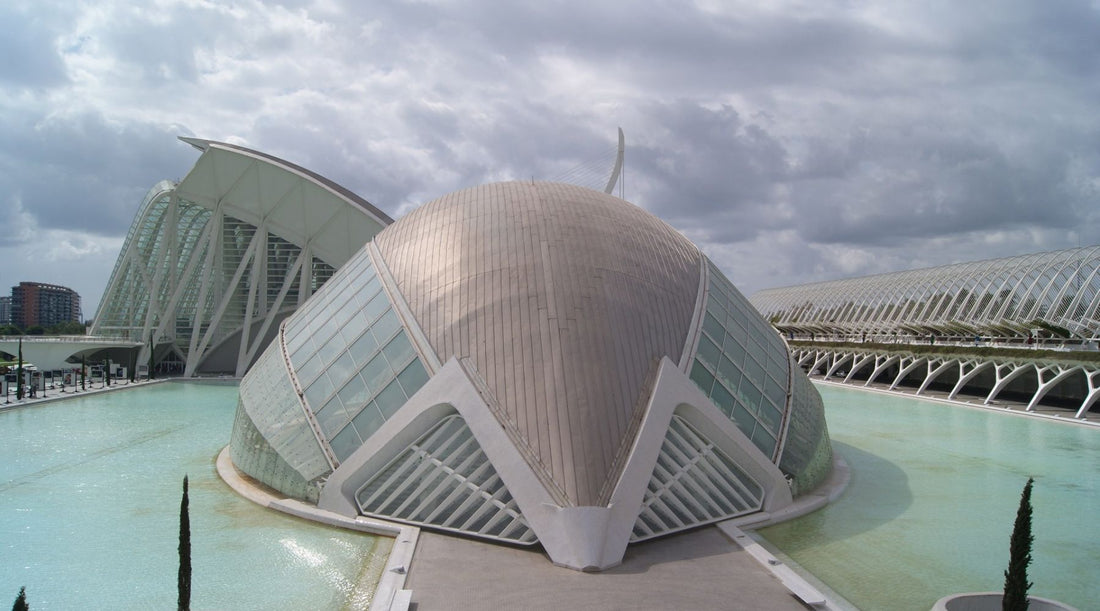
Construction Trends to Watch in 2025
Share
The construction sector is evolving rapidly to address pressing challenges and seize new opportunities. In 2025, expect significant strides in sustainability, digital innovation, workforce automation, adaptive designs, and supply chain efficiency.
Here’s a detailed breakdown of these transformative trends, real-world examples, and the potential benefits:
1. Sustainable Construction Practices: The push for environmentally friendly construction is reshaping materials, methods, and goals.
- Eco-Friendly Materials: Builders are increasingly using low-carbon concrete, recycled steel, and cross-laminated timber (CLT). For example, Milwaukee’s Ascent tower, the world’s tallest timber structure, combines reduced carbon emissions with remarkable structural benefits, such as high strength-to-weight ratio and exceptional seismic resilience, alongside aesthetic advantages. The use of cross-laminated timber (CLT) in its construction not only provides a lightweight yet durable framework but also enhances fire resistance due to the material’s charring properties, which form a protective barrier during exposure to flames. Bio-based options like hempcrete and mycelium panels are becoming mainstream, offering natural insulation and significant reductions in embodied carbon.
- Case Study: Norway’s Mjøstårnet building demonstrates how CLT can achieve high-rise construction standards while cutting carbon emissions by 30% compared to traditional materials.
- Positive Outcome: Reduced environmental impact, improved thermal efficiency, and increased marketability to environmentally conscious investors.
- Energy Efficiency: Standards like Passive House emphasize airtight construction and high-performance insulation to minimize energy use. Advanced features such as energy recovery ventilators and solar-integrated panels have created homes that produce more energy than they consume. A notable example is the University of Maryland’s 2017 Solar Decathlon entry, the reACT house, which integrated advanced solar technology, water recycling systems, and smart home features. The reACT house demonstrated the potential for zero-energy homes by generating a surplus of renewable energy while maintaining a comfortable and sustainable living environment.
- Case Study: Solar Decathlon-winning projects highlight the potential of zero-energy homes with integrated renewable technologies.
- Positive Outcome: Lower energy bills, improved indoor air quality, and compliance with stricter energy regulations.
- Circular Building Concepts: Material passports ensure components can be reused instead of discarded. Companies like Skanska integrate circular economy principles by reclaiming materials like steel and glass during demolition, reducing waste and resource extraction.
- Case Study: Skanska’s redevelopment of London’s Battersea Power Station incorporated recycled materials, cutting construction waste by 25%.
- Positive Outcome: Long-term cost savings, reduced landfill use, and compliance with ESG standards.
2. Digital Twins and Advanced BIM: Digital technology is revolutionizing project planning and management.
- Dynamic Planning: Digital twins—virtual replicas of projects—enable real-time adjustments and optimize decision-making. Sydney Metro uses this technology to monitor construction schedules dynamically, avoiding delays and cost overruns. For instance, digital twins are employed to simulate various construction scenarios, allowing the team to anticipate bottlenecks and adjust resource allocation in real-time. This approach has enabled precise forecasting of material needs, improved coordination among contractors, and minimized downtime caused by unforeseen events, such as weather disruptions or supply chain issues.
- Case Study: Heathrow Airport deployed digital twins to simulate and resolve passenger flow bottlenecks during terminal expansions.
- Positive Outcome: Improved project accuracy, reduced risk of delays, and better resource allocation.
- IoT-Enhanced Insights: Smart buildings like Amsterdam’s Edge use IoT sensors to feed real-time data into digital twins, enabling precise adjustments to lighting, ventilation, and energy use.
- Case Study: The Edge reduced its energy consumption by 70% through automated systems powered by IoT.
- Positive Outcome: Lower operational costs, enhanced tenant satisfaction, and minimized environmental impact.
- Lifecycle Optimization: Predictive analytics in tools like IBM’s Maximo allow for proactive maintenance. Facility managers can foresee and prevent failures, extending the lifespan of assets.
- Case Study: The Minneapolis Bridge integrated digital twin technology to monitor stress points, ensuring timely maintenance and preventing costly repairs.
- Positive Outcome: Reduced downtime, lower maintenance costs, and increased infrastructure resilience.
Automation and AI are transforming workflows, improving safety and efficiency.
- Autonomous Machinery: AI-driven equipment like Caterpillar’s graders and excavators streamline tasks with precision. Drones conduct site surveys, reducing survey time from weeks to days. For instance, the California High-Speed Rail project utilized drones to survey hundreds of miles of terrain, significantly expediting the process. These drones captured high-resolution topographical data, which was then integrated into planning models, enabling precise route alignment and minimizing project delays.
- Case Study: Boston Dynamics’ Spot robot performed inspections at Hyundai’s facilities, identifying potential safety hazards without human intervention.
- Positive Outcome: Faster project completion, enhanced accuracy, and improved worker safety.
- AI-Optimized Schedules: Platforms like ALICE Technologies analyze variables such as labor, weather, and material availability to create flexible schedules.
- Case Study: A Dubai skyscraper project reduced construction time by 15% using AI-driven planning tools.
- Positive Outcome: Reduced delays, better resource management, and increased profitability.
- Robotics in Action: Robots like SAM100 automate bricklaying, completing tasks up to six times faster than human workers. Similarly, autonomous welding robots ensure precision in critical infrastructure projects.
- Case Study: The Hudson Yards development in New York used robotics for repetitive tasks, reducing labor costs and improving site safety.
- Positive Outcome: Higher productivity, reduced worker fatigue, and fewer workplace accidents.
Adaptable and durable designs address climate challenges and shifting demands.
- Flood Resilience: Projects like Venice’s MOSE barriers protect cities from rising tides. Elevated homes with waterproof basements are becoming the norm in flood-prone areas.
- Case Study: New Orleans’ elevated homes program reduced flood damage costs by 40% during recent hurricanes. These homes feature elevated foundations ranging from 5 to 15 feet above ground level, incorporating reinforced concrete pilings and flood-resistant materials for walls and flooring. Design elements include waterproof basements with drainage systems that redirect water flow, ensuring minimal damage during floods. Additionally, many homes are equipped with elevated utilities and backup power systems, enabling quicker recovery for residents. The program has not only enhanced safety but also significantly lowered insurance premiums for participating homeowners.
- Positive Outcome: Improved disaster preparedness, reduced insurance premiums, and safer communities.
- Earthquake Safety: Advanced damping systems, such as those in Tokyo’s Skytree, absorb seismic shocks. Retrofitting older buildings with base isolators is gaining traction in regions like California.
- Case Study: The retrofit of San Francisco City Hall with base isolators protected the structure during recent earthquakes.
- Positive Outcome: Enhanced structural integrity, longer building lifespans, and reduced reconstruction costs.
- Modular Flexibility: Prefabricated units for hospitals and schools ensure scalability and rapid deployment. During health crises, these structures can be expanded or reconfigured quickly.
- Case Study: The Nightingale Hospitals in the UK were constructed in record time using modular techniques.
- Positive Outcome: Faster emergency response, cost-effective expansion, and adaptable infrastructure.
Efficient supply chain management reduces delays and ensures transparency.
- Blockchain Integration: Blockchain platforms like Provenance.org provide traceability, ensuring ethical sourcing and reducing disputes over material origins.
- Case Study: Turner Construction used blockchain to verify sustainable sourcing for a high-rise project in Chicago. Through this system, materials such as certified low-carbon concrete and ethically sourced steel were tracked throughout the supply chain. By ensuring real-time traceability, disputes over material origins were virtually eliminated, reducing project delays by 15%. The technology also simplified compliance with environmental certifications, bolstering client confidence and ensuring alignment with stringent ESG criteria.
- Positive Outcome: Improved accountability, faster procurement, and strengthened client trust.
- 3D Printing: ICON’s 3D-printed homes demonstrate how lead times and material waste can be drastically reduced. Custom components like intricate facades are now feasible at lower costs.
- Case Study: A social housing project in Mexico used 3D printing to deliver affordable homes in under a month.
- Positive Outcome: Reduced construction time, lower costs, and innovative design possibilities.
- Local Sourcing: Procuring materials locally not only minimizes delays but also reduces environmental impact. During the COVID-19 pandemic, projects that relied on local suppliers faced fewer disruptions.
- Case Study: Hudson Yards prioritized local sourcing to maintain schedules despite global supply chain challenges.
- Positive Outcome: Lower transportation emissions, faster material delivery, and stronger regional economies.
Final Thoughts:
The future of construction is defined by innovation and adaptability. Sustainable practices, advanced technologies, and resilient designs are not just trends but necessities for success. Companies embracing these changes are poised to lead the way in building a more efficient, durable, and eco-friendly world. By prioritizing these strategies, the industry can meet evolving challenges and create long-term value for stakeholders.