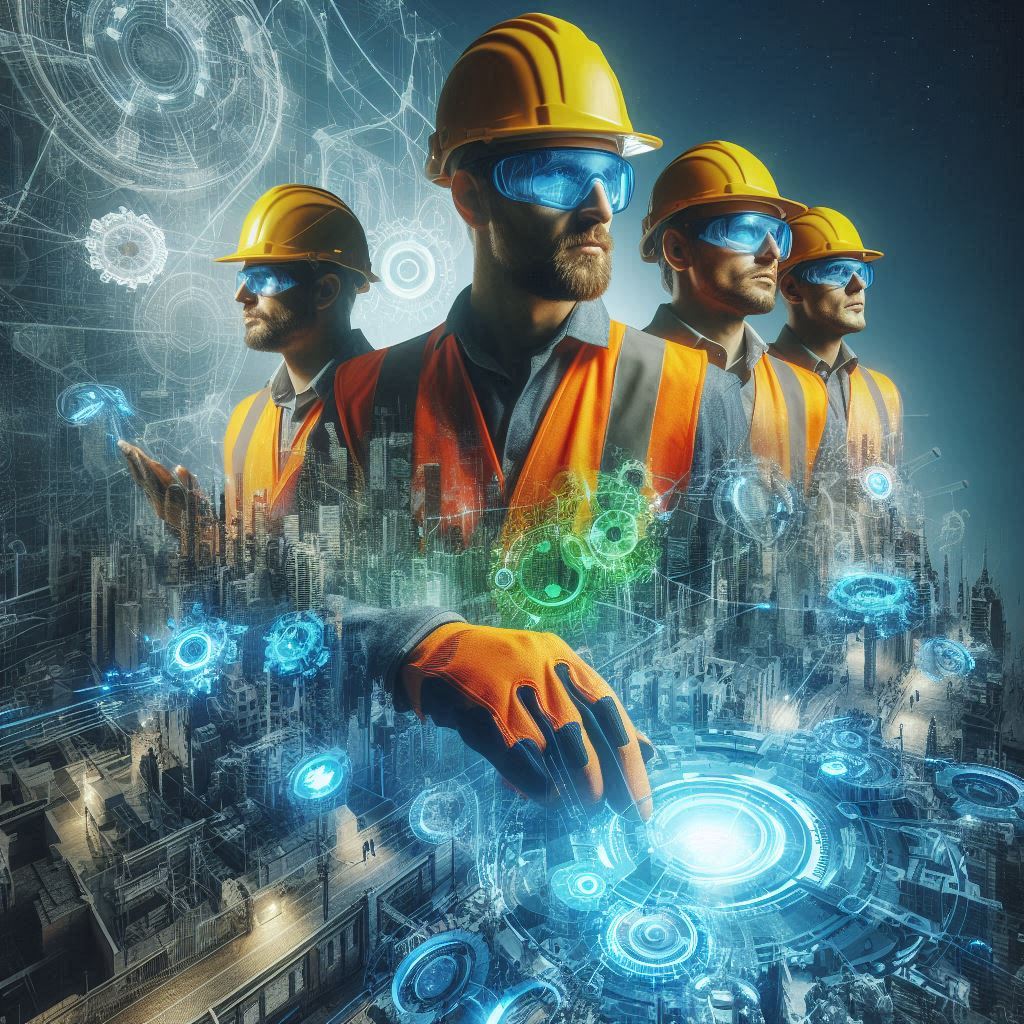
Construction 2.0: 5 Game-Changing Trends
Share
The construction industry is undergoing a profound transformation. Once seen as a field dominated by manual processes and conventional practices, construction today is being reshaped by emerging trends and advanced technologies. Digitalization, robotics, artificial intelligence, sustainable materials, and modular approaches are no longer futuristic concepts—they are the driving forces behind a revolution that is streamlining operations, reducing costs, enhancing safety, and improving project outcomes.
In this article, we explore five key pathways through which emerging trends and technologies are transforming the construction industry. We examine how these strategies work together, supported by real-world case studies, to redefine what is possible on the jobsite. Whether you are a contractor, engineer, architect, or developer, understanding and embracing these trends will be critical to thriving in tomorrow’s construction landscape.
1. Digital Transformation: BIM and Digital Twins
The Transformation
Digitalization is at the forefront of construction innovation. Building Information Modeling (BIM) has evolved from a mere 3D visualization tool into a central hub for collaboration. Today’s BIM systems integrate design, scheduling, cost estimation, and facility management into one cohesive digital model. Complementing BIM is the concept of digital twins—dynamic virtual replicas of physical structures that enable real-time monitoring, predictive maintenance, and performance optimization throughout a building’s life cycle.
By merging BIM with digital twin technology, construction teams can simulate a project’s entire lifecycle before breaking ground. This integration allows for the detection of design conflicts, optimization of energy usage, and the improvement of safety protocols. Digital twins provide an up-to-date view of construction progress, alerting managers to potential issues and ensuring that every stakeholder is aligned on the project’s objectives.
Actionable Strategies
Early Integration: Adopt BIM at the design phase and maintain an updated digital twin throughout the project lifecycle.
Real-Time Monitoring: Utilize sensor data and IoT devices to feed real-time information into the digital twin.
Collaborative Platforms: Use cloud-based BIM solutions to allow designers, contractors, and owners to collaborate seamlessly.
Predictive Analytics: Leverage digital twin data to forecast maintenance needs and optimize operational performance.
Case Study: The Sydney Metro Transformation
In Sydney, the Metro project integrated BIM with digital twin technology to manage one of the city’s largest infrastructure undertakings. By developing a comprehensive digital twin of the entire metro network, project managers were able to simulate various operational scenarios, optimize energy usage, and schedule maintenance before issues arose on the actual network. The result was a 20% reduction in downtime and significant cost savings over the project’s lifespan. This approach not only enhanced safety but also improved collaboration among multiple contractors and design teams, ensuring the project met stringent regulatory standards.
2. Robotics and Automation: Paving the Way for Efficiency
The Transformation
Robotics and automation are rapidly emerging as critical tools in the modern construction arsenal. The integration of automated machinery—such as drones for aerial surveys, robotic bricklayers, and autonomous excavation equipment—is revolutionizing jobsite operations. These technologies are not designed to replace human expertise; rather, they augment it by taking over repetitive, dangerous, or time-consuming tasks.
Automated systems offer higher precision, reduce human error, and dramatically improve productivity. Drones can capture high-resolution images and 3D scans of construction sites, ensuring accurate data collection and efficient progress monitoring. Meanwhile, robotic systems such as self-operating excavators or bricklaying robots are cutting down labor costs and speeding up construction timelines.
Actionable Strategies
Deploy Drones: Use drones for regular site inspections, progress tracking, and hazard detection.
Invest in Robotic Systems: Implement automated machinery for repetitive tasks like bricklaying, excavation, and concrete pouring.
Integrate with Digital Platforms: Connect robotics systems with BIM and digital twins to feed real-time data into project management software.
Continuous Training: Ensure the workforce is trained to work alongside robotic systems, emphasizing safety and efficiency.
Case Study: Komatsu’s Smart Construction Initiative in Japan
Komatsu, a global leader in construction equipment, launched a Smart Construction initiative in Japan that integrated autonomous machinery and robotics on a major infrastructure project. By employing self-operating excavators and drones for site surveys, the project saw a 30% increase in efficiency. The initiative also reduced on-site accidents by automating high-risk tasks. Contractors reported that real-time data from the drones allowed for quicker decision-making, ultimately saving millions of dollars in potential rework and delays. The project has become a benchmark for robotic integration in construction, showcasing how technology can enhance both safety and productivity.
3. Artificial Intelligence and Data Analytics: Smarter Decisions, Better Outcomes
The Transformation
Artificial intelligence (AI) is transforming the construction industry by providing actionable insights that drive smarter decision-making. From project planning and cost estimation to safety management and predictive maintenance, AI-powered analytics are reshaping how construction projects are managed.
Machine learning algorithms analyze historical and real-time data to predict potential delays, cost overruns, or safety incidents. AI tools can optimize scheduling, resource allocation, and even design iterations. Moreover, these systems help in risk management by forecasting issues before they become critical, allowing for proactive intervention.
Actionable Strategies
Predictive Maintenance: Use AI to analyze equipment data and predict failures before they occur.
Optimized Scheduling: Implement AI-driven project management tools that adjust timelines based on real-time variables such as weather and labor availability.
Cost Forecasting: Leverage machine learning to generate accurate cost estimates and identify opportunities for savings.
Risk Management: Deploy AI systems to monitor jobsite conditions and alert managers to potential hazards or delays.
Case Study: IBM Maximo on a Large-Scale Infrastructure Project
A major highway expansion project in California implemented IBM Maximo, an AI-driven asset management system, to monitor and manage heavy equipment and infrastructure conditions. The system analyzed sensor data from machinery and structural elements to predict maintenance needs, reducing unexpected breakdowns by 40%. AI-based scheduling tools also helped optimize workforce deployment, leading to a 15% improvement in overall project timelines. This case demonstrated how AI and data analytics could transform construction project management by enhancing both operational efficiency and safety.
4. Sustainable Construction: Eco-Friendly Materials and Processes
The Transformation
Sustainability is no longer optional in construction—it’s a necessity. The push toward eco-friendly building practices has led to the adoption of innovative materials and processes that reduce environmental impact while maintaining high-quality standards. Emerging trends include the use of mass timber, self-healing concrete, and 3D-printed components made from recycled materials.
Green construction not only minimizes waste and reduces carbon emissions but also often results in structures that are more energy-efficient and durable. Advances in material science have given rise to bio-based building materials and recycled composites that lower the overall environmental footprint of a project.
Actionable Strategies
Adopt Green Materials: Incorporate sustainable materials such as cross-laminated timber (CLT), recycled steel, and bio-based composites.
Implement Energy-Efficient Processes: Utilize technologies like 3D printing to reduce material waste and energy consumption.
Measure Carbon Footprint: Use digital tools to assess and manage the embodied carbon of construction materials and processes.
Leverage Renewable Energy: Integrate solar panels, wind turbines, and other renewable energy sources into construction projects.
Pursue Certifications: Aim for green building certifications (LEED, BREEAM) to validate sustainable practices.
Case Study: Stockholm Wood City, Sweden
Stockholm Wood City is a groundbreaking project spearheaded by Atrium Ljungberg that aims to build the world’s largest city entirely from timber. This ambitious initiative leverages mass timber construction to reduce carbon emissions significantly. By replacing traditional concrete and steel with cross-laminated timber, the project not only speeds up construction times but also minimizes environmental impact. According to research from Aalto University, extensive use of wood in construction can sequester millions of metric tons of CO₂ per year. This project has set a new benchmark in sustainable construction and demonstrates how eco-friendly materials can drive transformation while enhancing urban livability.
5. Modular Construction and Prefabrication: Faster, Safer, and More Flexible
The Transformation
Modular construction and prefabrication represent a shift from traditional on-site building to off-site manufacturing. This approach involves assembling components in controlled factory environments and then transporting them to the construction site for rapid assembly. Modular construction improves quality control, reduces construction waste, and cuts project timelines dramatically.
By standardizing and streamlining construction processes, prefabrication can address labor shortages and improve safety. Additionally, 3D printing is increasingly being integrated with modular methods to create complex components quickly and efficiently. The combination of modular construction with digital design tools ensures precision and flexibility, allowing for customizations without sacrificing efficiency.
Actionable Strategies
Invest in Off-Site Manufacturing: Develop partnerships with modular construction firms to manufacture key building components off-site.
Use 3D Printing for Custom Parts: Integrate 3D printing technology to produce complex components that can be easily assembled on-site.
Standardize Processes: Create standardized designs and processes to ensure consistency and reduce on-site errors.
Improve Logistics: Use digital tracking systems to manage the transportation and assembly of prefabricated components.
Enhance Quality Control: Conduct quality checks in the controlled factory environment to ensure high standards are maintained.
Case Study: Ireland’s 3D-Printed Social Housing Initiative
In Dundalk, County Louth, Ireland, a groundbreaking project showcased the power of modular construction combined with 3D printing technology. Three families recently moved into Ireland’s first 3D-printed homes, which were constructed using prefabricated concrete modules. The 3D printing process reduced construction time to just 12 days, and the entire project was completed in a fraction of the time required by traditional methods. The initiative, a collaboration between Louth County Council, Harcourt Technologies, and local construction firms, not only demonstrated significant cost and time savings but also provided high-quality, sustainable housing. The success of this project has sparked interest in rolling out similar schemes nationwide, highlighting the potential of modular construction to address housing crises efficiently.
Conclusion: Embracing the Future of Construction
The construction industry is at a pivotal moment, transforming rapidly under the influence of emerging trends and technologies. Digital tools such as BIM and digital twins, robotics and automation, AI-driven analytics, sustainable materials, and modular construction are reshaping how buildings are designed, constructed, and maintained. These five pathways work together to create a more efficient, safer, and sustainable industry.
By embracing digital transformation, construction firms can enhance collaboration and reduce errors. The integration of robotics and automation improves efficiency and safety on the jobsite, while AI and data analytics offer predictive insights that drive better decision-making. Sustainable construction practices not only benefit the environment but also provide long-term economic advantages, and modular construction enables faster, more flexible project delivery.
The case studies from Sydney Metro, Komatsu’s Smart Construction initiative, IBM Maximo implementations, Stockholm Wood City, and Ireland’s 3D-printed homes underscore that these emerging technologies are not just theoretical—they are being successfully applied in real-world projects. They serve as powerful examples of how innovation in construction can deliver tangible benefits for stakeholders, reduce environmental impacts, and address labor challenges.
For industry leaders, the message is clear: invest in and adopt these transformative technologies to remain competitive and drive the future of construction. The convergence of digital, robotic, AI, and sustainable innovations is not a distant dream—it is the reality of today’s construction landscape. By taking proactive steps to integrate these trends, companies can build smarter, faster, and more sustainably, ensuring that the structures they create are resilient, efficient, and future-proof.