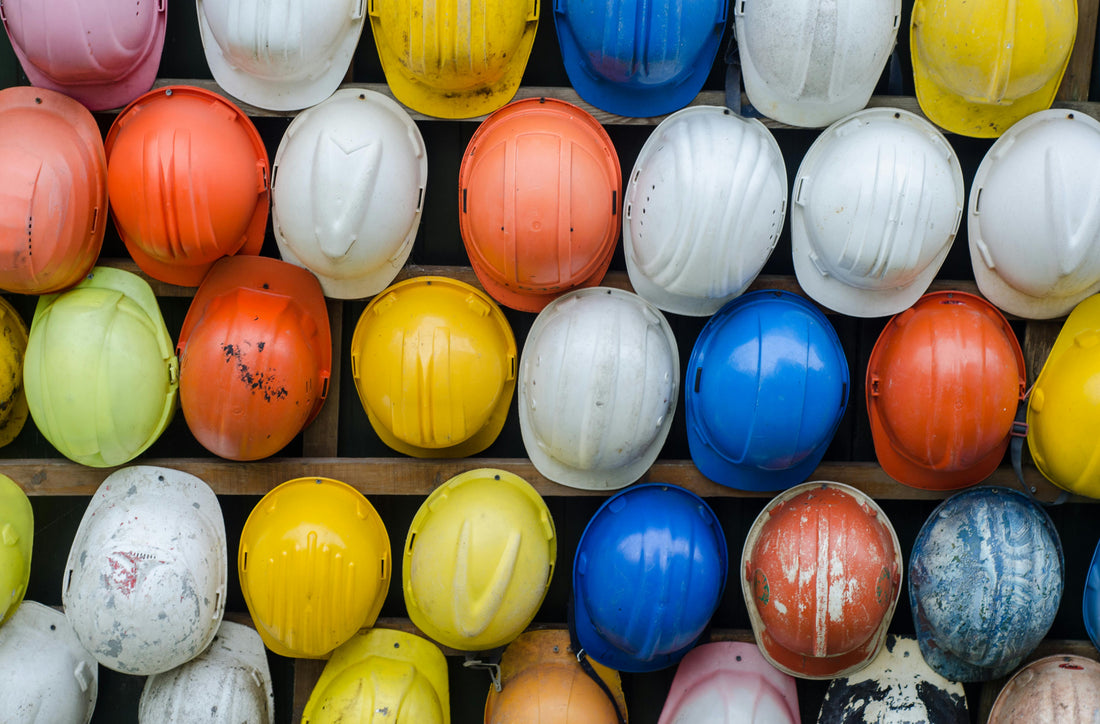
6 Ways Design Teams and Contractors Can Work Better Together for Owner Success
Share
6 Ways Design Teams and Contractors Can Work Better Together for Owner Success projects come in on time, within budget, and with the quality and innovation that build lasting value. In this article, we explore six critical ways that design teams and contractors can enhance collaboration, backed by case studies that demonstrate proven success.
1. Early and Continuous Collaboration
Why It Matters: Involving contractors in the design phase can eliminate many issues that typically arise during construction. Early collaboration helps identify potential challenges, streamline workflows, and enable value engineering from the outset. When contractors and design teams work together from the beginning, they can align on project objectives, budget constraints, and schedule requirements, ensuring that design concepts are practical and buildable.
Early involvement reduces surprises. Contractors can advise on material choices and construction techniques that may lower costs or accelerate the schedule. Design teams benefit from practical insights that can lead to innovative solutions. This level of cooperation builds a foundation of trust and mutual respect, making it easier to address problems as they arise.
Action Steps:
- Engage Early: Include contractors in pre-design meetings. Encourage participation during concept development to ensure design feasibility.
- Hold Joint Workshops: Organize collaborative sessions to brainstorm solutions to potential challenges.
- Establish Shared Goals: Align on objectives such as cost, quality, and schedule. Ensure all parties understand the owner’s vision.
- Utilize Integrated Platforms: Use collaborative project management tools to track changes and decisions from the earliest stages.
- Schedule Regular Reviews: Set up checkpoints throughout the design and construction phases to assess progress and address issues promptly.
Case Study: The Riverside Medical Center Project In a high-profile project in Texas, the Riverside Medical Center, design firm Apex Design and contractor Summit Construction began collaborating during the concept phase. By involving Summit Construction early, Apex Design was able to modify complex design elements that initially threatened to exceed budget constraints. Through a series of joint workshops, both teams developed a plan that reduced material waste by 15% and shortened the project timeline by four weeks. Regular design reviews helped pinpoint challenges before they escalated, resulting in a project delivered on schedule and within budget. The owner, Riverside Health Group, praised the collaborative process, noting that early contractor input was key to achieving their vision of a state-of-the-art facility.
2. Clear Communication Protocols
Why It Matters: Effective communication is the lifeblood of any successful project. Miscommunication between design teams and contractors can lead to costly delays, rework, and frustration. Clear communication protocols ensure that all parties are on the same page regarding project expectations, milestones, and changes. It minimizes misunderstandings and reduces the risk of conflict, both of which directly impact the owner’s satisfaction.
Establishing dedicated communication channels and regular touch points allows for timely updates and transparent decision-making. This ensures that any potential issues are flagged and addressed quickly, which is essential in keeping the project moving smoothly.
Action Steps:
- Define Communication Channels: Use platforms such as email, video conferences, and construction management software for real-time updates.
- Schedule Regular Meetings: Hold weekly or biweekly meetings where design and construction teams can discuss progress, challenges, and changes.
- Document Discussions: Keep detailed minutes and records of decisions made to avoid misinterpretation later.
- Assign Liaisons: Appoint a communication liaison on both sides who is responsible for coordinating updates and ensuring messages are clear.
- Implement a Feedback Loop: Encourage continuous feedback and allow for adjustments in communication practices based on team input.
Case Study: The GreenTech Office Complex In Chicago, the GreenTech Office Complex project encountered several coordination challenges during early construction stages. Design firm UrbanForm and contractor Skyline Build recognized that miscommunication was causing delays and rework. They instituted a strict communication protocol: weekly update meetings, real-time progress tracking via a cloud-based platform, and clearly documented change orders. When a design discrepancy was detected in the mechanical systems, immediate communication between both teams enabled a swift resolution. The design team revised the layout while the contractor adjusted installation plans, avoiding a major delay. The owner, Metro Holdings, credited this disciplined communication approach with keeping the project on track and reducing overall costs by 8%.
3. Integrated Project Delivery (IPD)
Why It Matters: Integrated Project Delivery (IPD) is a collaborative approach that brings the owner, design team, and contractor into a single contractual and operational framework. This model aligns the interests of all parties by sharing risks and rewards. In an IPD setup, every stakeholder is invested in the project’s success, resulting in a more efficient, transparent, and cooperative process.
IPD fosters an environment where innovations are encouraged and problems are addressed collectively. It minimizes adversarial relationships and focuses on joint problem-solving. For the owner, this translates to fewer disputes, fewer change orders, and ultimately a more successful project outcome.
Action Steps:
- Adopt IPD Contracts: Transition from traditional contracts to IPD agreements that clearly define shared goals and responsibilities.
- Establish Joint Governance: Create a project steering committee with representatives from each party to facilitate decision-making.
- Set Unified Metrics: Agree on success metrics that measure quality, schedule adherence, and cost performance.
- Share Information Openly: Use a common data environment where all teams have access to project information and updates.
- Promote Collaborative Culture: Encourage team-building and joint problem-solving sessions to foster a culture of mutual accountability.
Case Study: The Metro Transit Hub Project In Los Angeles, the Metro Transit Hub project was delivered using an IPD model. The owner, Los Angeles Metropolitan Transportation Authority (Metro), worked closely with design firm Innovate Designs and contractor Unity Constructors. This IPD framework allowed all parties to share design innovations and risk. When unexpected geotechnical challenges arose, the joint project team collaborated to develop an innovative foundation solution that saved both time and money. This integrated approach reduced project delays by 20% and cut cost overruns by 15%. Metro officials highlighted that the IPD model was a decisive factor in the project's success, citing improved transparency and accountability as key benefits.
4. Utilizing Technology and BIM
Why It Matters: Modern construction projects rely heavily on technology to enhance collaboration and streamline processes. Building Information Modeling (BIM) is a digital tool that creates a shared, 3D model of the project, enabling design teams and contractors to collaborate in real-time. BIM allows stakeholders to visualize the project before construction begins, identify potential clashes, and simulate various scenarios to optimize the build.
Using technology such as BIM minimizes errors, reduces rework, and improves overall project efficiency. It serves as a single source of truth for all stakeholders, ensuring that everyone is working from the same, up-to-date information.
Action Steps:
- Adopt BIM Early: Incorporate BIM in the design phase and extend its use throughout the project lifecycle.
- Train All Stakeholders: Ensure both design teams and contractors are proficient in using BIM software and related collaborative tools.
- Leverage Clash Detection: Use BIM to identify and resolve conflicts between different systems (e.g., structural vs. MEP).
- Maintain a Centralized Model: Keep a master model updated with all changes and accessible to everyone involved.
- Integrate Other Technologies: Combine BIM with project management software for seamless scheduling, cost tracking, and document control.
Case Study: University Research Facility At a new university research facility in Boston, design firm Nexus Architects partnered with contractor Precision Build to implement a full BIM process. By digitizing every element of the project, the teams were able to detect clashes between the electrical and plumbing systems before they became on-site issues. The BIM process also allowed the teams to simulate different construction sequences, which helped refine the schedule and reduce on-site disruptions. The project was delivered with zero significant rework and a 10% reduction in overall costs. The owner, Beacon University, commended the partnership for its innovative approach and the clarity it brought to an otherwise complex project.
5. Fostering Mutual Trust and Respect
Why It Matters: Trust and respect are the cornerstones of successful collaboration. When design teams and contractors view each other as partners rather than adversaries, they are more likely to work together to solve problems and improve outcomes. Mutual trust leads to greater transparency, fewer conflicts, and a more efficient project execution process. For the owner, this means fewer surprises and a more harmonious project environment.
Building trust takes time and commitment. It requires clear expectations, accountability, and a willingness to listen to each other’s concerns. Over time, a strong relationship between design teams and contractors can result in smoother operations and better overall project performance.
Action Steps:
- Develop Clear Roles: Clearly define the responsibilities of each party to avoid overlaps and conflicts.
- Encourage Joint Decision-Making: Involve both teams in key decisions, particularly those that impact the project’s direction.
- Invest in Team-Building: Organize workshops and informal gatherings to build camaraderie and understanding among team members.
- Recognize Contributions: Celebrate joint successes and acknowledge the hard work of all parties involved.
- Establish Conflict Resolution Mechanisms: Create a clear process for addressing and resolving disputes quickly and fairly.
Case Study: The High-Rise Urban Renewal Project In New York City, the High-Rise Urban Renewal project brought together design firm Skyline Concepts and contractor Empire Builders. Despite the inherent challenges of a densely built environment, both teams maintained a strong relationship built on mutual trust. They established a joint leadership committee to handle all major decisions and set up quarterly team-building sessions. This proactive approach to relationship management resulted in a project completed with minimal conflict and high owner satisfaction. The owner, Cityscape Developments, noted that the trust between the design and construction teams was the key factor in overcoming unexpected challenges during construction.
6. Emphasizing Value Engineering and Flexibility
Why It Matters: Value engineering is the practice of reviewing designs and construction methods to maximize project value while minimizing costs. When design teams and contractors work together on value engineering, they can identify opportunities to improve efficiency and reduce waste without sacrificing quality. Flexibility in design and construction methods allows teams to adapt to changes in project scope or market conditions, a vital trait in today’s dynamic environment.
A flexible, value-driven approach ensures that the project remains aligned with the owner’s objectives. It also creates an atmosphere where innovation is encouraged, and every team member is focused on delivering the best possible outcome.
Action Steps:
- Conduct Joint Value Reviews: Regularly meet to discuss cost-saving measures and design modifications that maintain quality.
- Analyze Alternatives: Explore different materials, systems, and construction methods to find the optimal balance of cost and performance.
- Remain Adaptable: Accept that changes may be necessary as the project evolves, and be willing to revise plans accordingly.
- Monitor Market Trends: Keep an eye on material costs and labor availability to adjust plans proactively.
- Document Decisions: Maintain detailed records of value engineering sessions and decisions made, ensuring transparency for the owner.
Case Study: The Corporate Headquarters Redesign A leading corporate headquarters redesign in Atlanta, managed by design team Visionary Architects and executed by contractor Keystone Construction, demonstrated the benefits of value engineering. Early in the project, rising material costs threatened to push the budget over the agreed limit. The two teams held a series of value engineering sessions to identify alternative, cost-effective solutions without compromising on aesthetics or functionality. They chose to replace a traditional glass facade with an innovative insulated panel system that provided similar visual appeal and improved energy efficiency. This flexibility not only saved the project 12% in costs but also enhanced the building’s long-term performance. The owner, GlobalTech Industries, acknowledged that the collaborative approach in value engineering was instrumental in delivering a modern, efficient, and cost-effective headquarters.
Conclusion
Collaboration between design teams and contractors is not merely beneficial—it is essential for delivering projects that exceed the owner's expectations. By embracing early and continuous collaboration, establishing clear communication protocols, adopting integrated project delivery, leveraging technology, fostering mutual trust, and emphasizing value engineering, all parties can work together more effectively to ensure project success.
Key Takeaways:
- Early Collaboration avoids later conflicts and ensures design feasibility.
- Clear Communication minimizes misunderstandings and keeps the project on track.
- Integrated Project Delivery aligns all stakeholders under a shared vision and risk/reward structure.
- Technology and BIM streamline workflows and reduce on-site errors.
- Mutual Trust and Respect build the foundation for long-term success.
- Value Engineering and Flexibility allow for innovative solutions that meet budget and quality targets.
As the construction industry evolves, the need for close collaboration between design teams and contractors will only grow. Owners now demand projects that are delivered on time, within budget, and with the highest quality standards. By implementing these six strategies, firms can not only meet these demands but also create a competitive advantage that sets them apart in a crowded marketplace.
Call to Action: Design teams and contractors—it's time to break down silos and build stronger partnerships. Invest in joint training sessions, embrace modern technologies, and prioritize transparency at every step. By working together, you can transform challenges into opportunities, ensuring that every project is a success for the owner and a testament to what true collaboration can achieve.